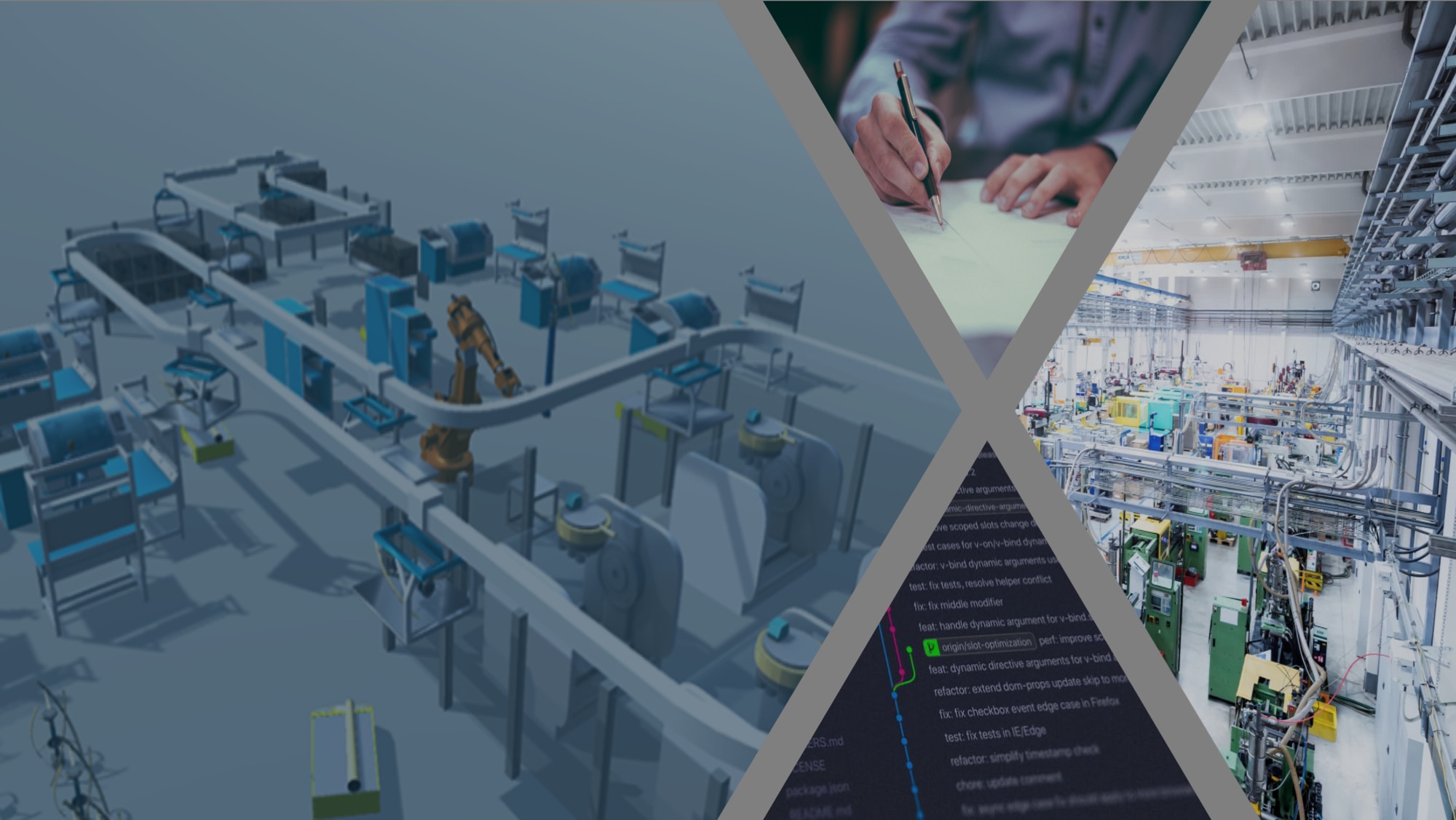
スマートマニュファクチャリング構築ガイドラインによるデジタル化
経済産業省が策定した『スマートマニュファクチュアリング構築ガイドライン』において、デジタルツインは製造業のデジタルトランスフォーメーションを加速させる重要な要素として位置づけられています。
本稿では、同ガイドラインを踏まえ、デジタルツインの概念とその製造現場における具体的な活用事例を紹介するとともに、多頻度データ収集やシミュレーションによる最適化など、ガイドラインで提唱される高度なデジタル化の実現に向けたCTCの取り組みを詳細に解説いたします。
目次[非表示]
スマートマニュファクチュアリング構築ガイドラインとシミュレーション
製造業での生産データ取得の拡大やIoT導入、工場のスマートファクトリー化によって、生産ラインや工場の「デジタルツイン」が実現しやすくなり、積極的な推進が試みられています。先月(2024年6月)、経済産業省から製造事業者各社が直面する経営課題の解決のための「スマートマニュファクチュアリング構築ガイドライン」が発表されましたが、その中ではシミュレーション等の活用によるデジタルツインを行うフェーズが定義され、より高度なデジタル化のための具体的な指針が用意されました。
例えば、Lv4の「多頻度解析による最適化」は、多頻度データ収集、シミュレーション等による意思決定材料の提示と最適解の探索・評価がされていることと定義され、最上位のLv5「現実との双方向連携」では、シミュレーション環境等で得た最適解に基づき現実のプロセスを制御している状態と定義されました。これにより、製造業事業者ごとによって異なる目指すべき実現レベルを探索・企画することが容易となりました。
スマートマニュファクチュアリング構築ガイドライン(経済産業省HPより):「スマートマニュファクチャリング構築ガイドライン」を取りまとめました (METI/経済産業省)
デジタルツインとは
デジタルツインは実際に稼働している生産ライン、もしくは新規建設予定の計画段階の生産ラインを仮想空間上にモデル化し、生産ラインの能力を評価や、将来的な動作予測や現場の運用オペレーションの事前検証のために利用されます。マシン設備を何台導入するのが最適であるか、半年後の納期に生産が間に合うかの予測、設備が故障した際の例外的なオペレーションの事前検討などが低コスト短期間に実現できます。
これまでもデータ分析やシミュレーションの活用によって部分的なデジタル化が行われてきましたが、デジタルに現場と同じ生産ラインを再現しさらには在庫や調達、配送などにも適用範囲を拡張することで、生産に関わる業務全体を考慮した最適化・効率化・性能評価が可能となります。
デジタルツイン導入・継続の難しさ
このように、デジタルツインは視野が広い分、幅広い範囲のエンジニアリングノウハウ、業務知識、さらにはデジタル技術・データ分析技術が必要となり、それらの専門知識の不足が導入の妨げとなります。また、一度仮想モデルを構築したとしても生産ラインの改修に合わせてモデルを修正する必要があります。モデルの維持のためには、運用に関わる多くの作業員への情報共有・教育が必要になることから、導入後の効果的な活用が困難となることも多いです。
生産上の多くの課題やデジタルで解決される余地がありますが、このような導入・継続の困難性によってデジタルツインの構築・積極的な活用まで至っていない製造業者も少なくありません。CTCでは30年以上にわたる生産現場のデジタル化推進経験から、現場の課題をデジタルで解決するための下記のような5つのフェーズを想定することで、スムーズな導入および長期的な活用を実現しています。
「課題設定」段階では生産ラインにおける現状の課題が明確でなく、データがほとんど取得できていない段階です。「アプローチ設定」では、データは取得蓄積されているが、課題解決のために効果的・効率的に活用できていない状態、「スポット活用」は部分的な活用にとどまり継続的な活用や全体最適化には至っていない状態を示します。この段階でもデジタル化の効果があらわれますが、「継続的活用」のような大規模・長期間の運用、さらにリアルタイム性・システム化を実現した「デジタルツイン」段階に到達することを目指し、ものづくり全体のプロセスの最適化へと変革のステージを引き上げることを目指します。
CTCが展開するIntelligentTwinサービスの姿
CTCでは以上のフェーズごとに、異なったサービス内容を定義しています。まず課題が定まっていない場合はお客様と一緒に課題設定やアプローチ方法の定義や目標の明確化を行います。この際必要となる技術要素は何なのかをツール起点でなく課題起点で発見し、シミュレーションや数理最適化、AIなど複数のアプローチを視野に技術アセスメントを行います。
一方、すでにデータ活用のアプローチが定まっている場合はPoCによって有効性を確認し、全体への拡張を見据えながらシミュレーションや最適化のスポット活用を推進します。ここで効果が確認された場合は、プロセス全体のデジタルツインやシステム構築に踏み込み、運用や教育まで含む一貫したご支援を行います。デジタルツイン構築や全体最適化をより積極的に推進していくために、上流の課題設定フェーズからデジタルツイン導フェーズまで一貫して取り組めるのはCTCの強みです。
おわりに
伊藤忠テクノソリューションズでは、『IntelligentTwinサービス』を展開しています。製造業を中心に多くの企業がデータの蓄積・活用先としてデジタルツインに積極的に取組んでいますが、「使用するデータが不足している」「取得できないデータがある」「分析技術が足りない」などの課題が挙げられます。
IntelligentTwinサービスでは、これらの課題に対して、AI、シミュレーション、数理最適化を組み合わせて、最適な価値を提供します。また、生産性向上や新規設備投資計画、人員配置最適化などの課題に対しては、適切な手法の選定から運用フェーズでのモデル精度維持まで、さまざまな形でご支援いたします。
【関連記事】