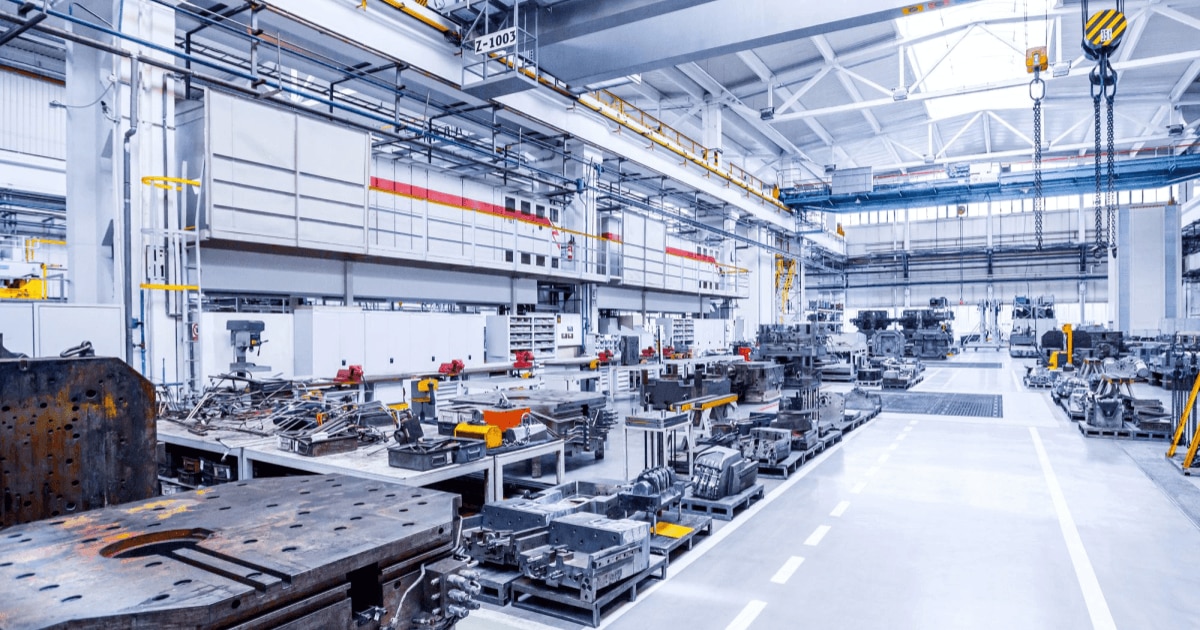
生産プロセスの最適化で生産性向上! 改善を図る3つの方法
製造業において重要な経営課題の一つに、生産性の向上が挙げられます。近年、市場ニーズの多様化や技術革新による製品の高度化、製品ライフサイクルの短縮化などによって、製造業を取り巻く環境が変化してきました。それに伴い、生産プロセスも複雑になりつつあります。
そうしたなか、以下のような課題が生まれやすくなってます。
「多品種少量生産での在庫管理や原価管理が難しい」
「仕様変更による組み換え作業でタイムロスが発生する」
「設備故障や不良品発生による機会損失を招いている」
このような課題を抱えている製造現場では、生産性の向上に向けて、生産プロセスの最適化に取り組もうと検討されている方もいるのではないでしょうか。
この記事では、製造現場での生産プロセスを最適化するメリットと改善方法について解説します。
出典:経済産業省『2016年版 ものづくり白書 | 第3節 市場の変化に応じて経営革新を進め始めた製造企業|その1』
目次[非表示]
最適化による生産プロセス改善の効果
最適化して生産プロセスを改善すると、以下の効果が期待できます。
- 生産効率の向上
- 品質の安定化
- リードタイムの短縮
- 在庫の余剰・不足の防止
生産プロセスを最適化すると、非効率な作業の改善が図れるほか、人材や設備、原材料などを必要最小限に抑えられるため、生産効率の向上が期待できます。
また、故障や不良が発生する工程・頻度を把握して対策したり、業務を標準化して作業員による作業手順のばらつきを解消したりすることで、品質の安定化、属人化防止にもつながります。
原材料や部品などの材料調達のプロセスを管理して、適切なタイミングで発注できるようになると、生産の着手がスピーディーになり、リードタイムの短縮も期待できます。
そのほか、需要予測を踏まえた生産計画を最適化することにより、在庫の余剰・不足を防いで、コストの削減につなげられます。
生産プロセスの改善を図るための方法とその効果
生産プロセスの最適化を図るには、現状の業務フローや作業内容を把握したうえで、問題のあるプロセスの改善を図ることが重要です。ここからは、具体的な改善方法とその効果について解説します。
①ボトルネック部分の洗い出し
生産プロセスを改善するにあたって、まずはボトルネックとなる工程や業務を洗い出すことが重要です。
生産工程が多くなると、工程ごとにかかっている工数・時間・稼働率などを把握することが難しくなります。そこで、シミュレーションを用いてボトルネック分析を行い、問題のある箇所の作業方法・手順・人員配置などを見直すことで、業務フローの短縮・業務効率の向上につなげられます。
▼業務フロー・作業手順の見直し例
- 作業手順を標準化して作業員による偏りを解消する
- 生産負荷がかかっている工程の人員を増員する
- 業務フローの統合・分割によって手待ち時間や複数回のやり取りをなくす
②AIやIoTによるデータ取得・分析
AIやIoTの技術を活用することで、製造現場にある生産設備・機器の稼働データを取得・分析して、業務工程の改善や品質管理などに役立てられます。
また、IoTにより仮想空間と実空間のデジタルツインを実現し、生産量予測や故障診断をリアルタイムで行えます。例えば、以下のような活用ができます。
▼AIやIoTによるデータ取得・分析の活用例
- IoTセンサーで取得した生産ラインの稼働率や作業員の作業効率を分析して、業務フロー・人員配置などを見直す
- 製造機械の温度・圧力・振動を計測するIoTセンサー・カメラから取得したデータを分析して、故障やメンテナンスの時期を予測する
- AIによる画像認識で製品の外観検査を行う
③生産プロセスシミュレーターの活用
IoTを用いて生産プロセス全体の状況を見える化した後、そのデータを用いて仮想空間上にシミュレーションモデルを作成することで、生産プロセスの改善を図ることができます。
▼生産プロセスシミュレーターの例
最適化アルゴリズムを用いることで、さまざまな条件(工程・制約条件・組み換え時間・サイクルタイムなど)の組み合わせから、最適な値を導き出せます。なかでもAIとシミュレーションを掛け合わせることで、より精度の高いモデルの作成が可能です。
▼生産プロセスシミュレーターの活用で把握できる内容例
- 製造機械の適正稼働率
- 作業場の適正な人員数
- 搬送機器の台数
- 適正在庫数 など
伊藤忠テクノソリューションズのIntelligentTwinサービス
伊藤忠テクノソリューションズでは、『IntelligentTwinサービス』を展開しています。
製造業を中心に多くの企業がデータの蓄積・活用先としてデジタルツインに積極的に取組んでいますが、「使用するデータが不足している」「取得できないデータがある」「分析技術が足りない」などの課題が挙げられます。
IntelligentTwinサービスでは、これらの課題に対して、AI、シミュレーション、数理最適化を組み合わせて、最適な価値を提供します。
その中で生産プロセス改善ソリューション『assimee』をご紹介します。assimeeはAIとシミュレーションを掛け合わせ、生産工程の最適な改善策を見つけるための強力なSaaSプロダクトです。
通常、シミュレーションモデルはさまざまな入力パラメータを要求します。 一方、assimeeは入力パラメータのデータ測定や準備が不要であり、AIが出荷データを再現するパラメータを推定します。理想のアウトプットを実現する工程の処理能力を高精度に求めることができるため、生産プロセス改善の意思決定をサポートすることができます。
またassimeeは直感的でわかりやすいUIを搭載しており、工程フローと処理能力を入力するだけでシンプルな生産ラインをスピーディーに分析することができます。そして、作成した製造プロセス全体の仮想シミュレーションモデルは一目でモデルの流れやシミュレーションの実行結果を確認できます。
生産性向上や新規設備投資計画、人員配置最適化などの課題に対しては、適切な手法の選定から運用フェーズでのモデル精度維持まで、さまざまな形でご支援いたします。
まとめ
この記事では、生産プロセスの最適化について以下の内容を解説しました。
- 最適化による生産プロセス改善の効果
- 生産プロセスの改善を図るための方法とその効果
生産プロセスを最適化すると、生産効率の向上や品質の安定化、リードタイムの短縮、在庫の余剰・不足の防止などのメリットが期待できます。
生産プロセスの改善方法には、シミュレーションを用いたボトルネック分析や、AI・IoTを活用してデータ取得・分析をしたりする方法が挙げられます。さらには、プロセスシミュレーターの活用が有効です。
伊藤忠テクノソリューションズでは、導入から運用まで様々な課題を解決するIntelligent Twinサービスを提供しています。
【関連記事】