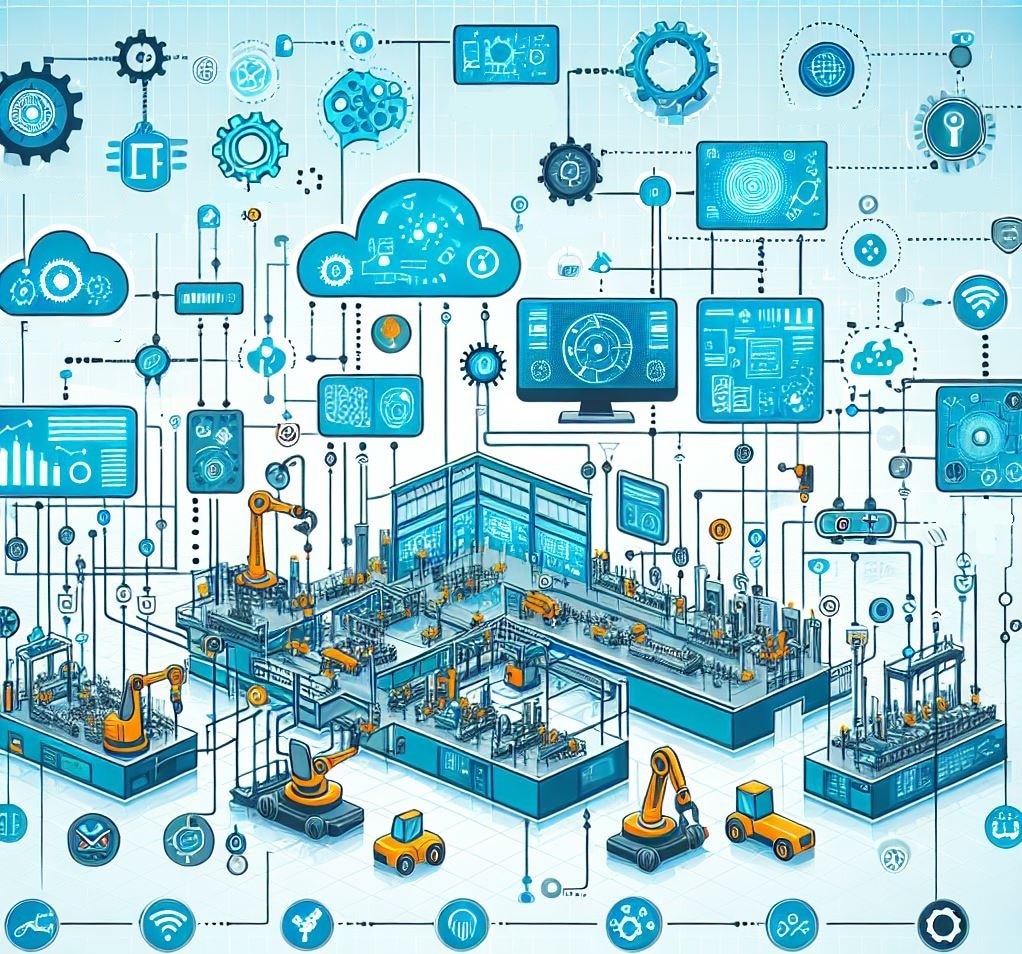
製造業デジタルツインの導入プロセス 課題解決から最適化までの道のり
はじめに
本記事では、生産・物流領域でのデジタルツインについて、推進にあたっての枠組みの提示および導入プロセスをご紹介します。デジタルツインは高度なDX活用にあたるため活用までの道筋を立てることが難しいですが、具体的な課題と段階的取組を提示しながら解説いたします。
目次[非表示]
スマートマニファクチャリングの取組み
製造業を取り巻く環境変化(自然災害、国際紛争、パンデミック、労働人口の減少、脱炭素化など)に対応するため、デジタル技術を活用して製造プロセスを最適化することが求められています。このデジタル技術を用いた全体プロセス最適化による意思決定支援の取組みはスマートマニファクチャリングと呼ばれています。
現状では多くの場合でデータ収集や解析は手動で行われ、意思決定も人間の勘と経験による部分が大きいです。これに対しスマートマニファクチャリングの予測・最適化段階では仮想空間上でシミュレーション・最適化を行い、その結果をもとに最終的な意思決定は人が実施します。デジタルツイン段階ではシステムがデータ基盤と連携し、リアルタイムにデータ収集および最適な生産計画を立案することを目指します。
デジタルツインと伴走支援
スマートマニファクチャリングの高度化領域となる予測・最適化やデジタルツインは初めて取組む場合も多く、実現するためには多くのハードルが存在します。また、データの準備からデジタルツインへ向けた取り組み方や、どこまで目指すのかによって必要な技術やコストが変わってきます。また、途中で新たな課題が発見されることもあり柔軟に取り組める体制作りも重要となります。CTCでは伴走支援IntelligentTwinサービスにより、各レベルの目指す姿に応じた最適な支援をご提供します。デジタルツインの導入は、段階的に進めることで効果的に実現できます。
よくある課題と導入効果
よくある課題として生産計画や人員配置など計画系の最適化や搬送機の能力や搬送レイアウト検証が挙げられ、下記のような要素が含まれる場合にはシミュレーションによるアプローチが有効です。
計画系の最適化
- 生産順序や人員のシフトスケジュール、在庫や配送計画など様々な計画
- 機械、搬送機などリソースを取り合うような動的な挙動
- 人員の作業能力のバラつきや機械の故障発生など不確定な要素
- 品種により工程フローが変わる、くり返し処理する工程が含まれる
搬送能力、レイアウト検証
- 製造プロセスの工程間搬送、工場や施設内の搬送、倉庫内の搬送やピッキングなど
- 有軌道や無軌道など様々なレイアウトによる搬送能力や渋滞状況の検証
- 在庫置き場の容量による搬送能力への影響
- 人や搬送機、輸送車など能力違いによる影響
シミュレーションの導入効果として、生産計画の最適化により従来比で10%以上の生産時間短縮が実現されています。また、搬送レイアウトや搬送能力の検証により無人搬送機の効率的な運用や故障による不測の事態への対策など様々な課題解決に活用されています。
伊藤忠テクノソリューションズのIntelligentTwinサービス
伊藤忠テクノソリューションズでは、伴走支援「IntelligentTwinサービス」を展開しています。本サービスでは30年以上にわたるプロセスシミュレーションや数理最適化技術の知見や経験を活かして、課題が漠然としている、どのようなデータが必要なのか、アプローチ方法が分からないといった初期段階のコンサルティングからシミュレーションや最適化による意思決定支援、デジタルツイン環境の構築・運用までCTCが伴走支援いたします。
将来の展望とリアルタイムシミュレーション
デジタル技術を用いた全体プロセス最適化による意思決定支援の取組みは仮想空間上に工場やラインを表現し、シミュレーションや最適化を行うことで実現できます。さらに仮想空間と実データと連携させ生産ライン上のボトルネックを可視化したり、実データをもとに将来の状況をリアルタイムにシミュレーションすることで、変化する状況に柔軟に対応して最適な生産計画や人員配置を実現します。
【関連記事】